冲压加工的质量标准与关键因素解读
作者:佚名|分类:百科常识|浏览:84|发布时间:2025-08-14
基本概念
-
质量: 指的是实体能够满足明确和隐含需求的总特性。
-
实体: 可以单独描述并研究的对象。
-
产品: 具体活动或过程的结果,包括硬件、软件、流程性材料、服务以及它们的组合。
-
自检: 由工作的执行者依据规定规则进行的工作检查,目的是判断完成的任务是否合格,并控制工作过程。
影响质量的主要因素
主要涵盖五个核心要素:
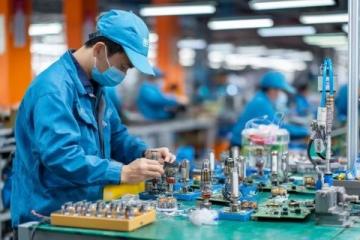
-
人员:涉及质量意识、责任心、操作技能、心理素质和专业水平等。
-
设备:包括设备的精度保持性、稳定性、可靠性以及配合间隙、定位和定量装置的准确性与可靠性等。
-
材料:关注原材料的化学成分和物理性能,以及配套件、元器件和零部件的外观或内在质量。
-
工艺方法:涉及工艺流程安排、工序间的衔接、加工手段选择和指导性文件制定。
-
环境条件:考虑生产现场的温度、湿度、噪音、振动、照明和室内清洁度及污染水平。
质量检验
质量检验包括对实体特性进行的测量、检查、试验和对比,判断其与规定要求的一致性,并确定每项特性的合格状态。此过程拥有以下关键职能:
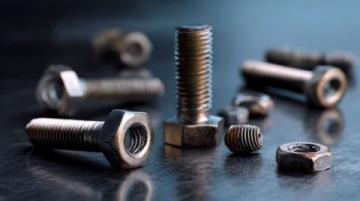
-
保证:确保产品的质量达到标准。
-
预防:通过检测发现并纠正潜在问题。
-
报告:提供数据以供评估。
-
监督:监控整个生产流程和产品质量。
按检验程序分类
-
进货检验:对原材料、外购件等进行质量检查,如冲压用的板料和卷料入库与开卷剪切过程中的检测。
-
工序检验(过程检验):在每个工序完成后进行的质量检查,包括自检、互检和专检。
-
最终检验(成品检验):对完成产品的质量进行全面评估。
质量问题的处理
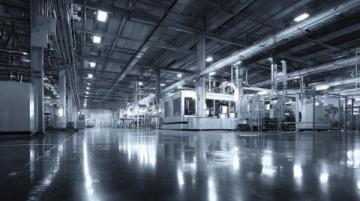
-
问题处理原则:遵循“三不放过”原则和逐级上报规则,旨在防止类似问题再次发生。
- “三不放过”包括原因查明、责任明确及预防措施落实的要求。
-
不合格品控制:
-
定义:没有满足既定标准或要求的产品视为不合格。
-
缺陷:不能满足预期使用需求或合理期望,特别是涉及安全的需求。
-
操作者在发现不合格产品时应采取以下步骤:
- 标识和隔离不合格品。
- 评估并评审产品的质量状况。
- 制定纠正措施以防止再发生问题。
不合格品的处理方式包括返工、返修、降级、报废或拒收等。
检验与试验状态
为了维持生产秩序,程序规定了产品四种不同的检验和试验状态,并赋予其特定的颜色标识:
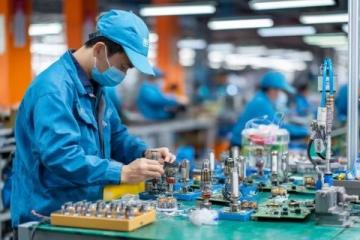
- 已检验合格的产品应标记为绿色。
- 正在检验但结果未确定的可使用黄色标识。
- 已被认定不合格的产品,返工或报废则分别用黄色和红色表示。
- 未经检验的产品需使用白色标识。
常见冲压缺陷及原因
-
落料与冲孔(修边):
- 毛刺过大、变形、表面划伤、尺寸不符或缺少孔眼等。
原因包括:凸凹模间隙不当、刃口磨损、导向精度差、凸凹模不同心,孔距太小、压料板与凹模型面配合不良、间隙过大,操作拖拉导致划伤,上料不准确或定位装置损坏等。
-
拉延:
- 包括开裂、起皱、表面损伤、波浪形、鼓包、凹坑、麻点等。
原因有:凸凹模R角半径小、压边力过大、材料成形性能差或尺寸偏大、间隙太小、润滑不当、定位不准,模具表面粗糙度不匹配或拉毛现象。
-
翻边:
- 表现为翻边不垂直、高度不一致、拉毛、裂纹等问题。
原因包括:凸凹模间隙过大、不均匀的尺寸偏差、定位不准确、落料件尺寸错误,刃口有伤痕或表面杂质,刃口硬度低等。
(责任编辑:佚名)